
Customer Testimonies
Group Vertical
Michigan Spring & Stamping
Haworth
Dematic
Lean solutions is trusted by brands including

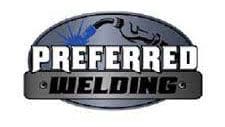
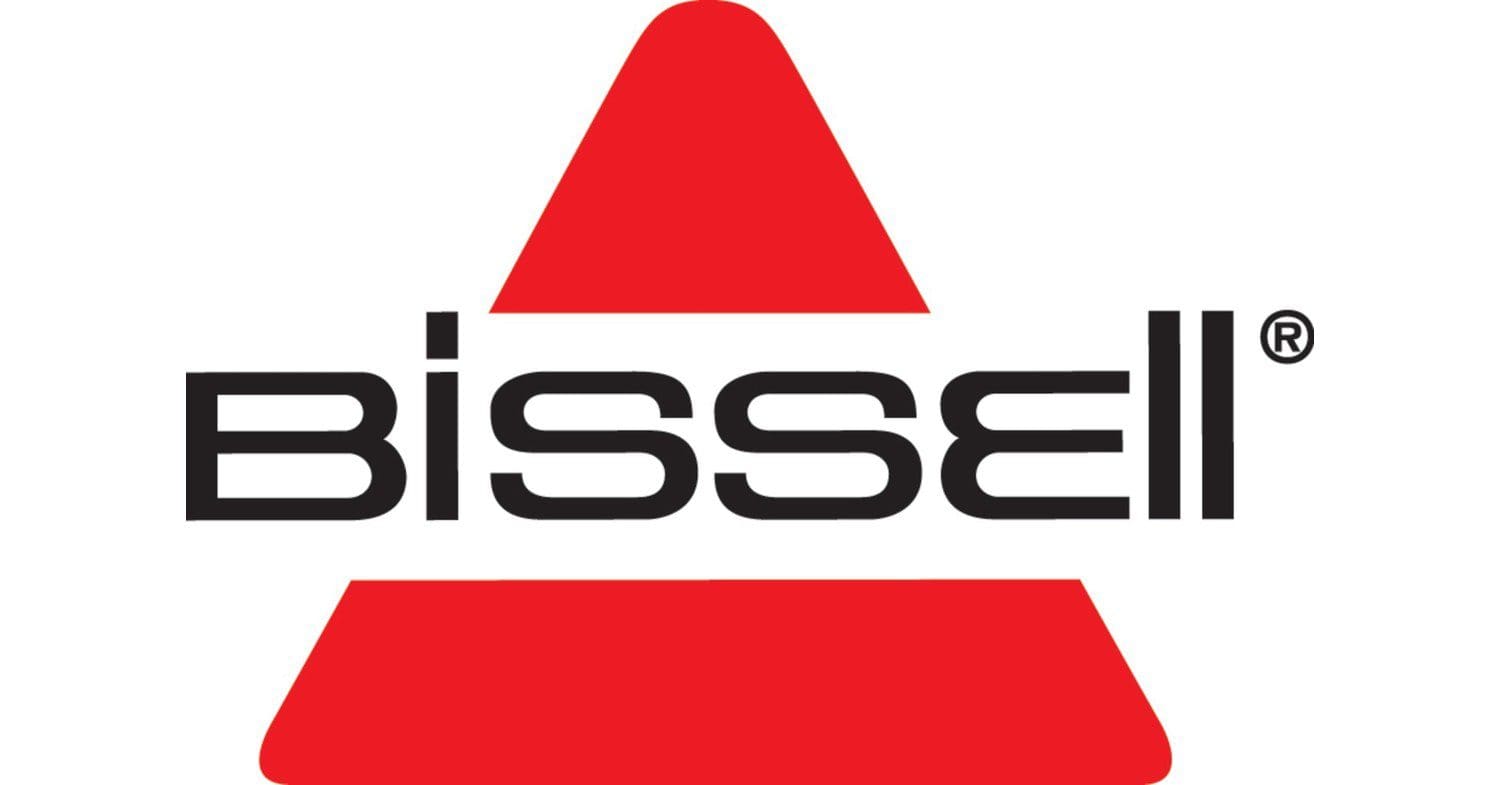

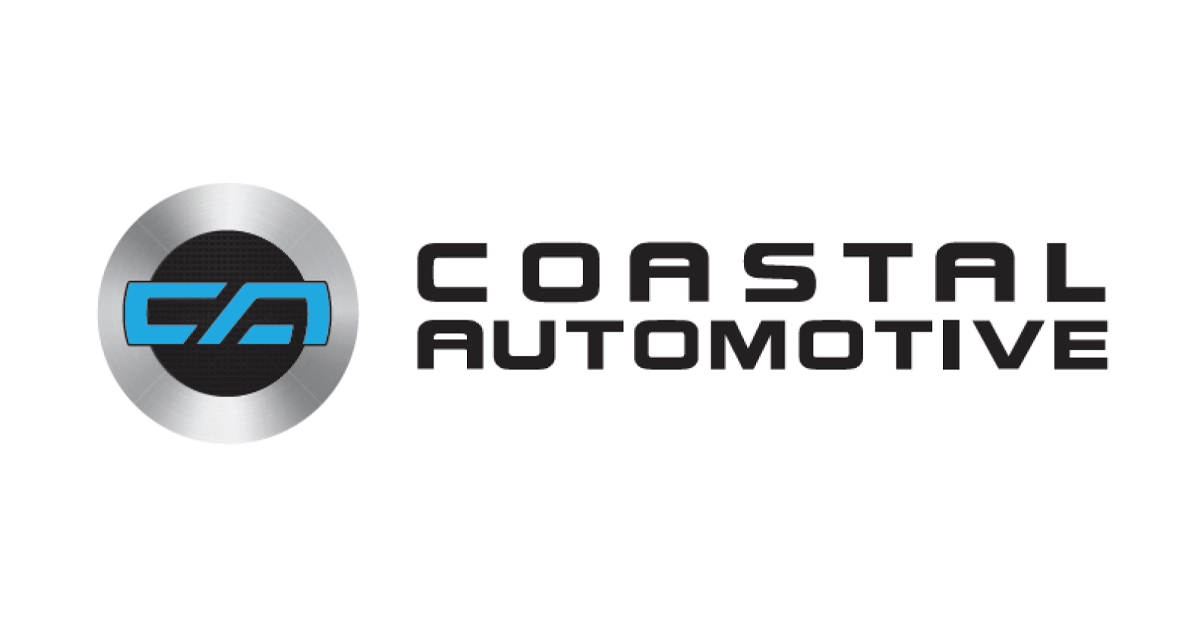

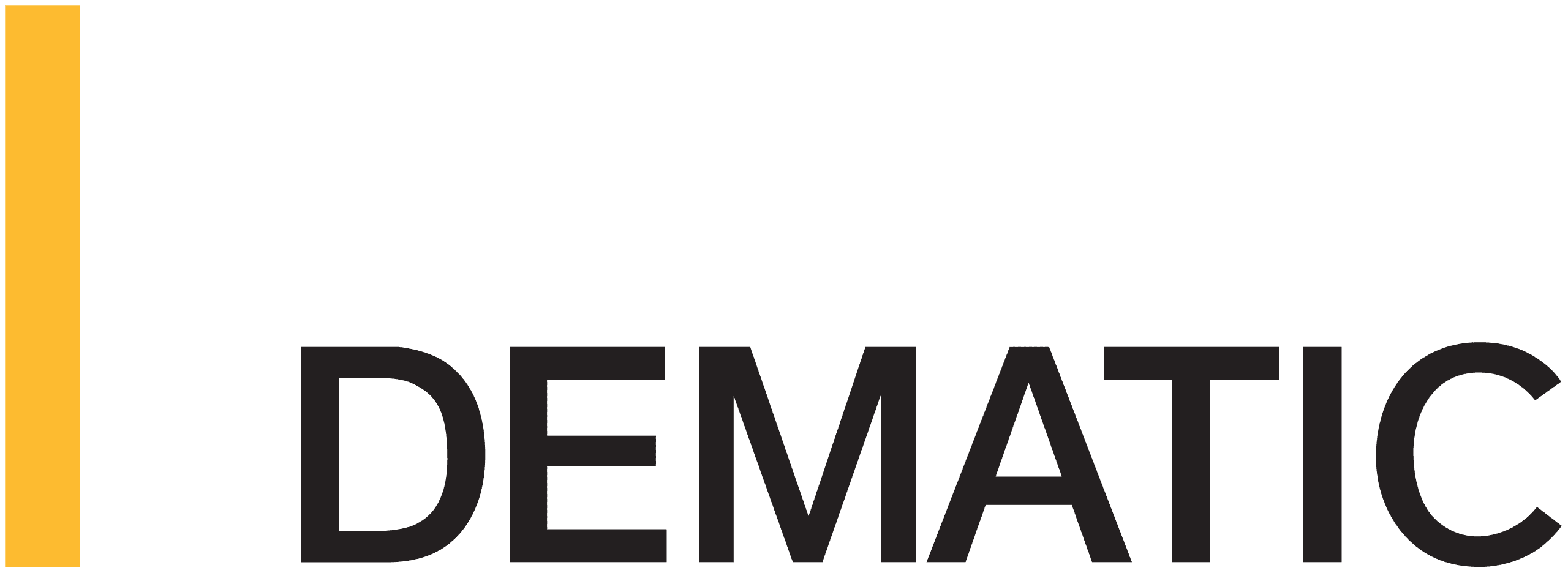

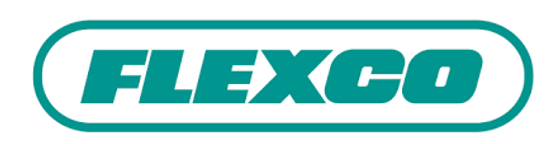
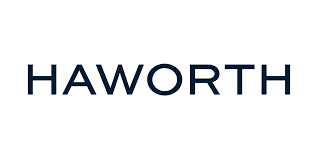

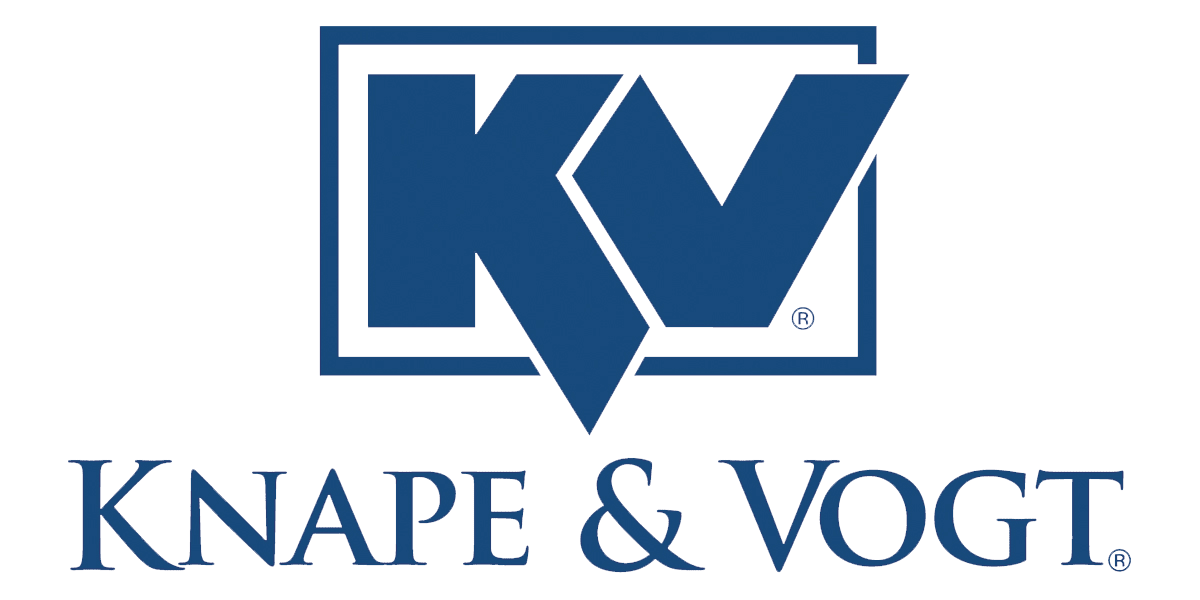
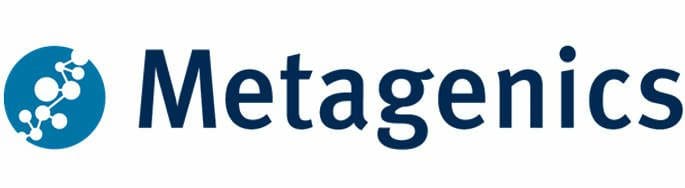

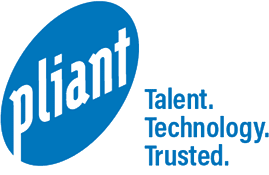



CASE Studies
Group Vertical
Group Vertical is a USA-based wholesale supplier of replacement screens and repair parts for Apple iPhones, Samsung, Motorola, and other phones. Our team partnered with Group Vertical over a 12-month period with initial goals to increase capacity by improving quality and reducing leadtime. After deploying lean and six sigma techniques, we were able to reduce leadtimes by 30% and improve supplier quality by 15% resulting in increased margins of 10% on A+ iphone screens. We also facilitated 6 kaizen events resulting in dramatic improvements to their processes. We recently carried out a two (2) day workshop delivering the 8-Steps to Crucial Conversations. This workshop was interactive and activity-based with break-out sessions and real-life scenario practical application.
Michigan Spring & Stamping
Michigan Spring and Stamping is a leader in the manufacturing of a diverse range of engineered metal components. They manufacture coiled springs, including compression, extension, torsion and garter springs, along with stampings, fourslide/multislide metal products, CNC wireforms, specialty rings and precision spring and stamped assemblies.
Michigan Spring and Stamping brought us in to develop and deliver a structured problem solving training and certification program. This program offered practical application, simulations, and one-on-one coaching. We carried out 4 sessions over a 6 month timeframe across multiple shifts. Each participant delivered individual projects resulting in over $200k in cost savings projects.
Haworth
Our team developed, trained, and deployed the Haworth Value Stream Management methodology which was rolled out across the entire company. We worked alongside their leadership team to develop a model value stream at a manufacturing site in Michigan which is now used as a benchmark for the rest of the company. We trained, developed and coached more than 100 leaders across 7 different manufacturing sites in daily management practices. Our team also facilitated implementation of a plan and coached leaders to eliminate a $7.5 million backlog in one of the manufacturing sites and improved daily schedule completion to a status of product due +1 day. This project alone resulted in above 95% on-time customer delivery for the first time in 9 years and allowed for the workforce, which had experienced an average of 50-57 hour work weeks, to work 40-44 hour consecutive weeks for the first time in 2 years.
Dematic
Our team partnered with Dematic to take existing training programs and curriculum, update them, and create refreshed and new curriculum to enhance and engage their workforce. As initially created, the curriculum was not giving them the hands-on components and did not offer the skills they were trying to teach. As part of the new curriculum, our team helped
create simulations that were practical allowing the learners to walk away knowing how to apply the learning in their daily jobs. We also delivered the curriculum (Lean Foundations and Structured Problem Solving) to over 300 Dematic employees over 6 months. We are now being asked to return to Dematic to assist their supply chain team in supplier development to increase capacity by improving operations.